March 8, 2021 | Rob Hirschberg
Alpine's 10-Step Battery Reconditioning Process
News Alerts & Updates
Join our email newsletter for industry trends, best practices, company news, & more.
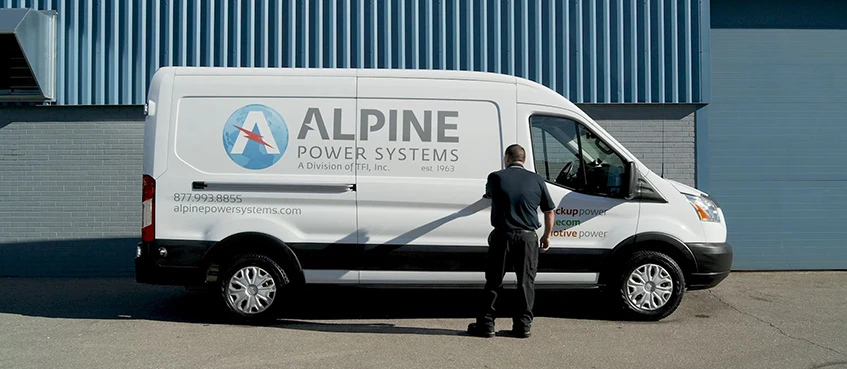
Share
Alpineās PowerMAX Fleet is the Nation's largest inventory of Premium Reconditioned Forklift Batteries. Alpineās Certified Pre-Owned Batteries go through a rigorous 10-Step reconditioning process to ensure the customer gets the best quality product available. Weāll take you through this 10-step reconditioning process that highlights how a PowerMAX Fleet Pre-Owned Battery stands out from the competition.
1. Visual Inspection
An Alpine Certified Technician will perform a visual inspection to take note of any noticeable problems with a forklift battery.
Symptoms of acid loss
Automatic watering systems
Corrosion
IC connector problems (Inter-cell connectors)
Signs of external arcing
Physical damage
2. Checking Voltage & Specific Gravity
Alpine's service team will assess battery health by testing the forklift battery's voltage and specific gravity. These tests help our team understand the battery's current healthĀ and how to best recondition the battery.
3. Wash & Neutralization
An Alpine technician will thoroughly wash the forklift battery with water and acid neutralization chemicals. This helps provide clean and safe working conditions and also takes away eventual surface voltage.
4. Cable & Jumper Assembly
The motive power technician will now find and fix the high resistance parts of the battery, apart from eventual cells. High resistance causes a drop in voltage and excessive heat development.
Typical Causes of High Resistance Include:
Loose screws or corroded IC connectors
Sulfated /corroded connections
Bad welds & Bad cables
5. Load Testing
Our service team member willĀ perform a full load test thereby measuring the forklift batteryās Ah capacity and study the results.
6. Cell Replacement
If the difference between cell capacity too large, than a cell replacement may be necessary.
7. Acid Adjustment
Sulfuric acid is added as needed by an Alpine team member. This is needed if acid hasĀ boiled out of the battery.
8. Equalization Charge
In this step we even out cell capacity with an additional equalization charge.
9. Equalization & Finish
10. Paint & Final Preparation
The forklift batteryās casing is sanded, and all corrosion is removed, then the forklift battery is painted with anti-corrosive and antioxidant paint, once the paint dries, stickers are added, the forklift battery is wrapped in a protective plastic film and is placed on and securely fastened to pallet. Now the forklift battery is finally ready for shipping.
Learn more about Alpine's state-of-the-art Forklift Battery Reconditioning Program: Click Here
Explore More Motive Power Articles